Optimal for process management in CVD/etching/ALD processes
CVD / ALD / Etching Process Model:RGM2-201F
ULVAC
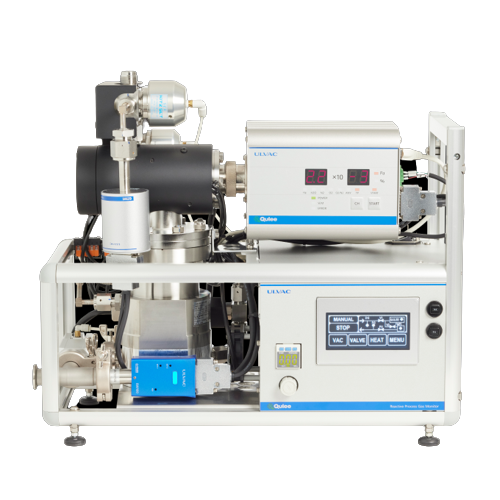
For more information on ULVAC products, purchase, and/or consideration, click here.
Features
- The exhaust system and the control system are integrated to realize vertical positioning, and the world's smallest footprint makes it possible to monitor reactive gases even in production lines with limited space.
- The replacement speed of filament kits during maintenance has been dramatically improved, and 120 minutes of work by 2 workers can be completed in 10 minutes by 1 person.
- Dual filament enables gas analysis without stopping the production line if the first filament breaks.
- Uses touch panel for real-time status checking.
- Operation from startup to measurement is complete only on the computer.
- The use of our company's unique Closed Ion Source with magnet enables long and stable measurement even during reactive processes.
- The highly sensitive ionization chamber with low gas dissociation enables highly sensitive gas analysis using only a Faraday cup.
- Compact channel control valve that prevents decomposition and adsorption due to thermal reactions.
- Reduces the distance from the process chamber to the ion source, enabling fast response decomposition.
- Enhances preventive maintenance functions
Preventive maintenance of ion sources and secondary electron multiplier tubes
Installation of tresability function of analytical tube (Patent No. 5016031) - The standard software is compatible with Windows 8/10/11.
Applications
In CVD/ALD/Etching equipment
- Monitoring of reactive gases during the process
- Endpoint monitoring of the etching cleaning process
- Residual gas measurement
Specifications
Sensor
Mass number range (amu) | 1~200 | |
Resolution (M/ΔM) | M/ΔM=1M(10%P.H.) | |
detector | Faraday Cup (FC) | |
Sensitivity (A/Pa) *1 | 1e-5A/Pa (Direct orifice installation, Ie=50uA) N2 gas =5e-4Pa at Ee50V |
|
Minimum detected partial pressure (Pa) *1 | e-10Pa (EE50V, Ie500uA) | |
Total pressure measurement function *1 | Yes. | |
Total pressure measurement range *1 | 1e-3 ~ e-6 Pa | |
ion source | Closed Ion Source with Magnet | |
filament | Ir/Y2O3 2 pieces (one of them is spare) | |
Ionization voltage (EE; eV) | 20~70eV (50 V setting is recommended for Ie50 uA) | |
Emission current (IE; uA) | 50uA/500uA (EE50V, 50uA recommended for process measurement) |
Differential exhaust system
Connecting flange | VCR1/2 "Osnut Equivalent | |
Specification pressure | Select from 0.5~30 Pa/10~500 Pa | |
Turbomolecular pump | UTM70B (70L/s) | |
Foreline pump | None ForealImport: KF16 Guaranteed operating foreline pressure: 500 Pa or less Pirani Vacuum Gauge for Foreline Pressure Checking: SW100-A |
|
Vacuum gauge for monitoring equipment pressure | Capacitance Manometer “Model:CCMT” |
Utilities
Power supply voltage | Select from AC100~120 V/6 A, AC200~220 V/3 A | |
Compressed air | Dry N2:0.4MPa |
Other
Mass | 20Kg | |
Control unit | touch panel | |
Block type heater unit | 110°C±10°C |